MonitorPro
Developed by: IRSA informatica
MonitorPro is a powerful and effective tool in distributing the work program to the production departments. The work orders to be carried out, foreseen by the company MRP system, are exploded in the single phases and addressed to the terminals of the production departments concerned.
In fact, it becomes a friendly interface of your MRP management, easy to use by both production managers and individual phase operators.
Advantages of using MonitorPro
It makes simple and flexible what by its nature is not, that is, the programming of production from MRP.
It transmits and requests the operator only what is strictly necessary to carry out the processing, in an immediate and flexible way.
It allows you to change the bill of materials and the cycles envisaged by the MRP during the course of work and returns the correct information to the management system without having to start over every small change in the cycle or bill of materials provided.
MonitorPro maintains a constant link between the single product line to be processed and the customer order that generated the requirement. The management of the article, on the contrary the one normally done by an MRP, is not anonymous, this even without having to create specific orders, thus reducing the process management time.
This system makes it possible to monitor the production status of the processed articles in real time, item by item, in each of its processing phases. How many pieces have been produced, compliance, waste, partial production, material and times actually used, information that is sent back to the MRP which closes the processing orders and realigns the warehouse situation of the materials produced and those actually used.
Technical features
The program is marketed in a Windows environment, and is designed to operate as an appendix to Zucchetti's AdHoc Enterprise, but it is also possible, upon request, to link it to other management software. MonitorPro can be installed both locally and on servers, the database must be installed on servers, terminals are required in the departments for the use of the program by phase operators, in this way the paper support is useless in the give orders to departments.
As for hardware, the requirements mainly depend on the type of use, but in general the processing and memory needs are not particularly heavy, and therefore it is compatible with all current computers. Printer: laser.
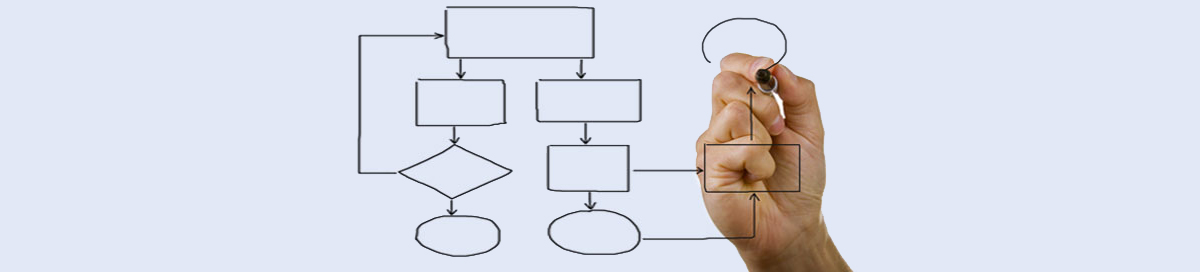
Work method
The program operates on 4 ways of viewing and managing the work program.
Card file mode
Shipping mode
Date mode (consultation)
Internal warehouse reordering mode
Card file mode
The card mode is the main entry mode, the customer orders are imported into MonitorPro grouped in Tabs and if the production cycles are present in the MRP archive, they are automatically assigned to the departments provided, otherwise the intervention is assigned to the manual. The departments can still be activated and deactivated manually with a simple check on the department, you can also change the quantity to be produced at any time within MonitorPro which will take care of realigning the situation with the MRP automatically.
For each article it is possible to give additional inputs, adding notes to the description inherited from the MRP.
In this mode, as for all the others, the production manager sees and manages the situation of all the departments, the heads of groups of phases see only the steps of their competence, the operator sees only the items associated with the phase of his interest.
In the same assignment console, the managers can see the progress of the processes, with quantities produced, compliance, materials used, actual times, any waste and all feedback entered by the operator. Feedback is very precious as it becomes a historical memory for that type of processing that can be recalled at any time it must repeat itself.
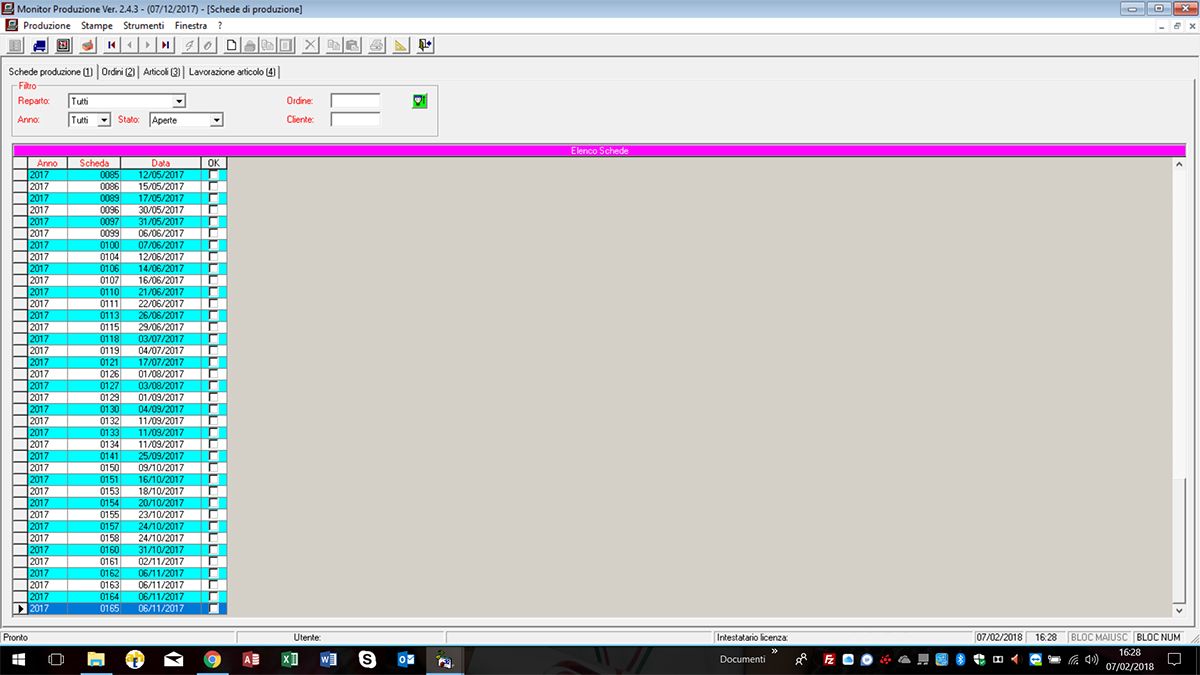
Shipping mode
The shipping mode is a powerful and useful tool to support logistics, in this section transport for customer deliveries is planned and managed. The carriers to be used are established, the actual delivery date which will influence the production date and time to optimize the transport itself.

Single orders can be grouped into one shipment or split into multiple shipments. Grouped orders will travel hand in hand, even in internal logistics, until the final shipment.
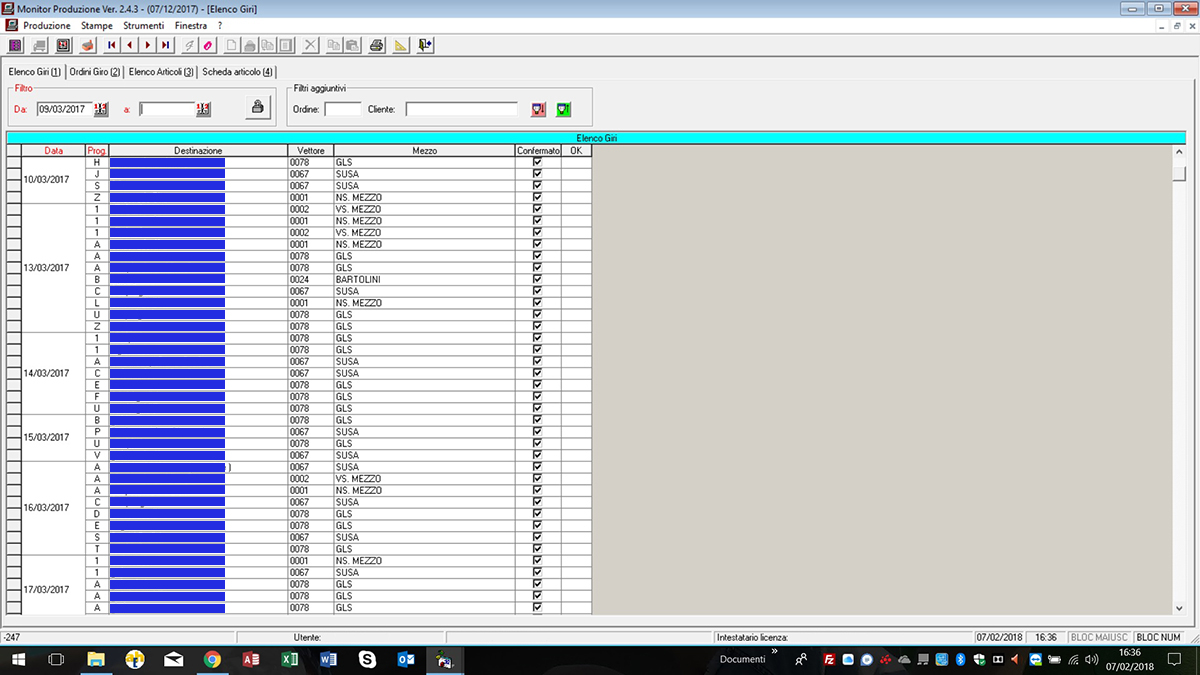
Date mode (consultation)
This is the mode mainly used by phase operators, here you have the list of articles to be produced sorted by production date and time, the operator only sees the articles assigned to its phase.
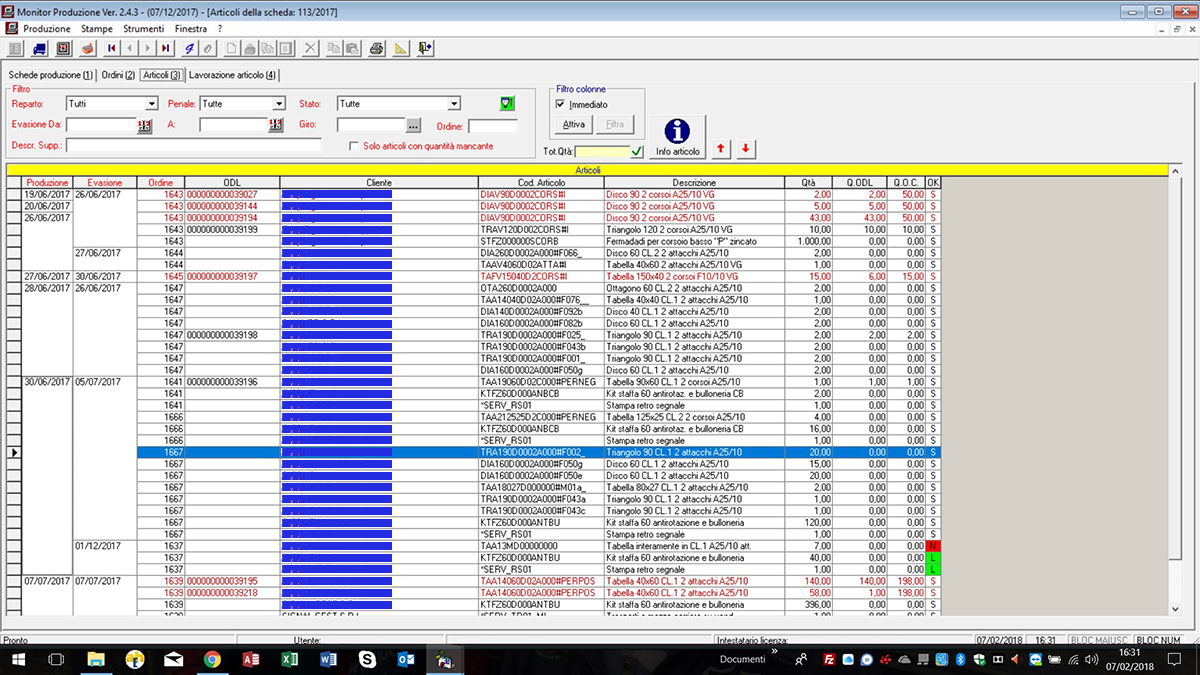
By clicking on the article you go to the detail where there is the information on the material to be produced, which derive from the MRP, processed in the card mode and the quantities currently produced of the same article in the previous phases are also visible in real time.
It is in the article detail that the operator must enter the information relating to his work, he can confirm the quantity produced if equivalent to that requested or declare a partial production, declare any product waste and conformity. Indicate the name of the operator who carried out that particular phase, confirm the material used provided by the bill of materials, which is proposed upon exiting the detail page, since it can possibly be modified if for some reason it was necessary to operate differently from the provisions of the standard list.
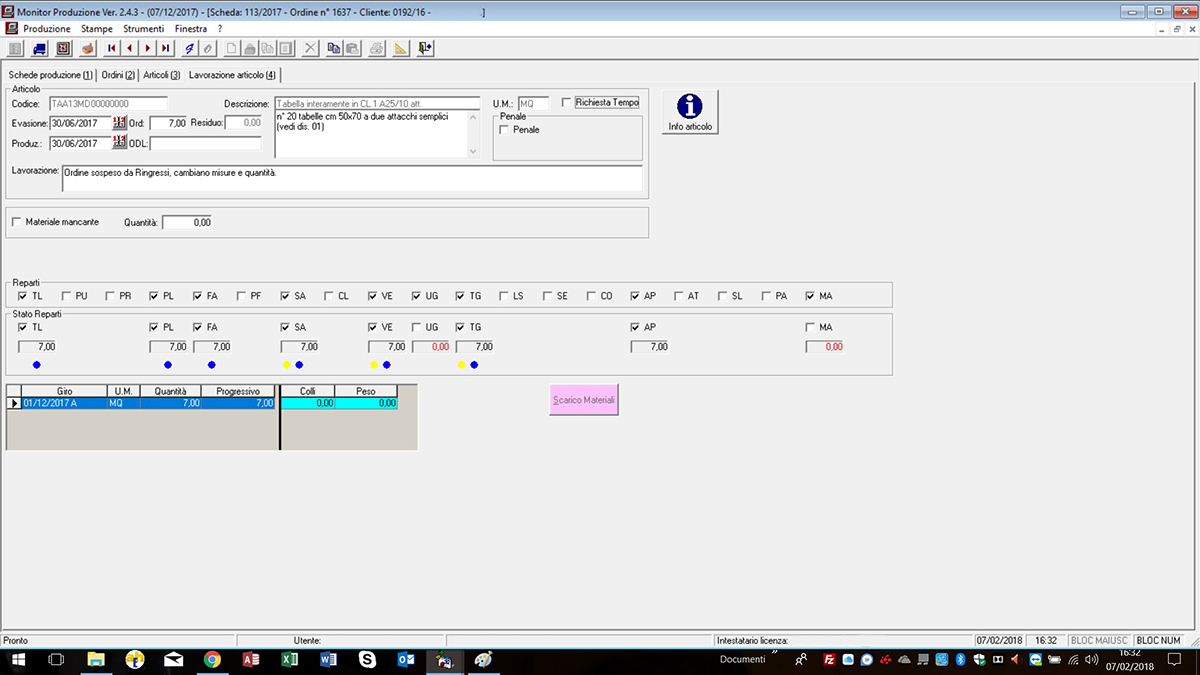
This mode is also very useful for the managers of the various sectors, as, as for the others, there are powerful filters that allow searches and groupings for each element present in the database, customer, order, article, production date, status of production etc.
At any point of the program, by positioning on an article and clicking on the information button, it is possible to immediately see the warehouse situation of the article and that of all its components, including orders and orders from other articles.
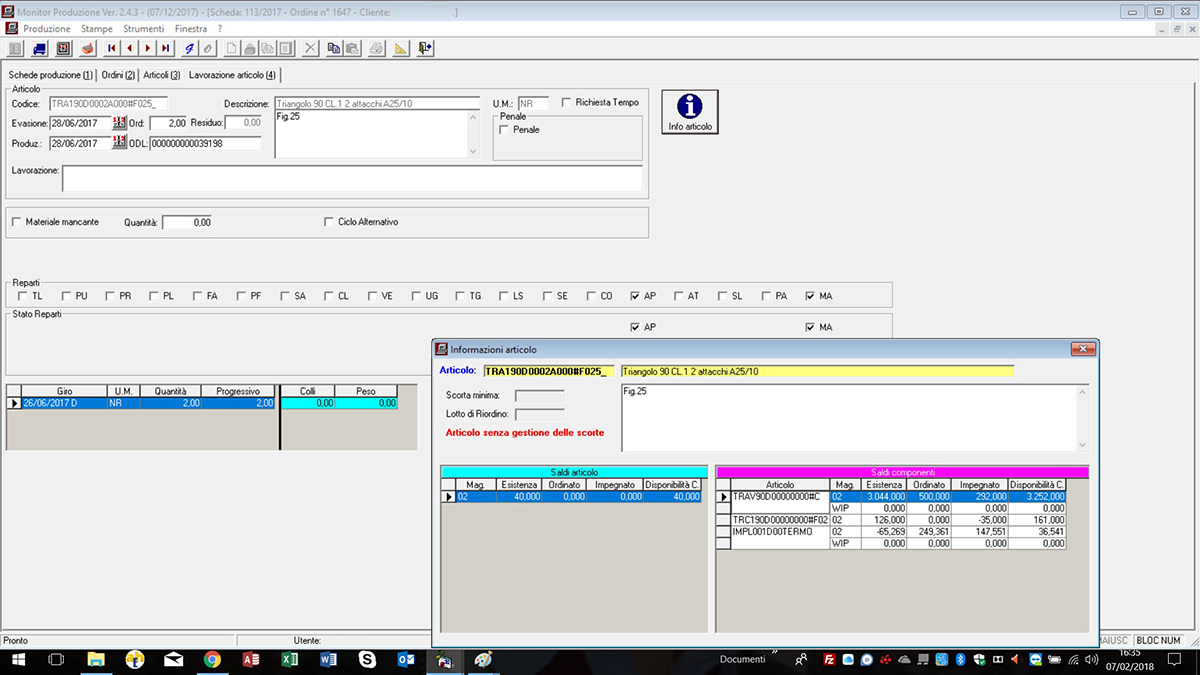
Internal warehouse reordering mode
This mode brings together the card and date mode in a single tool that deals with the items managed on stock on the management system, the need for which was generated by a condition of warehouse under-availability. The reordering methods are those established by the management system, processed by the MRP, the management is equal to that of the items whose requirements were generated directly by the customer order.
